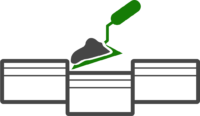
Methods of Concrete and Foundation Repair
What if you could raise a cracked or sunken slab back to its proper level in less than an hour, with no “down” time waiting for new concrete or mortar to cure?
There are only three choices when it comes to repairing a settled or sunken concrete slab: replace it, grind it, or raise it. Before the use of polyurethane and Poly jacking, the common methods of raising and supporting a slab was by mudjacking.
Following is a brief description of the options to consider when you're raising a sunken slab.
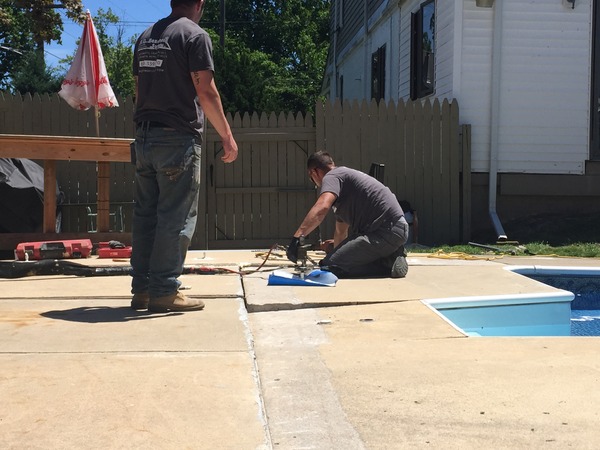
Poly Jacking
Mudjacking
Grinding
Replacement
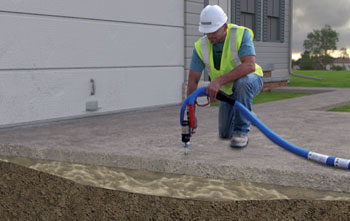
Poly Jacking, also called Foam jacking, lifts and raises settled slab foundations by injecting high density polyurethane foam under the slab, where it expands and pushes the slab back into place. The lifting is gentle and over a large area at once, which helps to ensure the most complete lifting of all the methods.
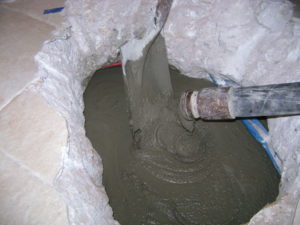
Mudjacking, also called Slabjacking, lifts and raises settled slab foundations by pumping sand-based grout under the slab. The mechanical force of the pump pushes the slab back into place. Mud jacking tends to be pretty messy, and is best used for unoccupied areas of the home.
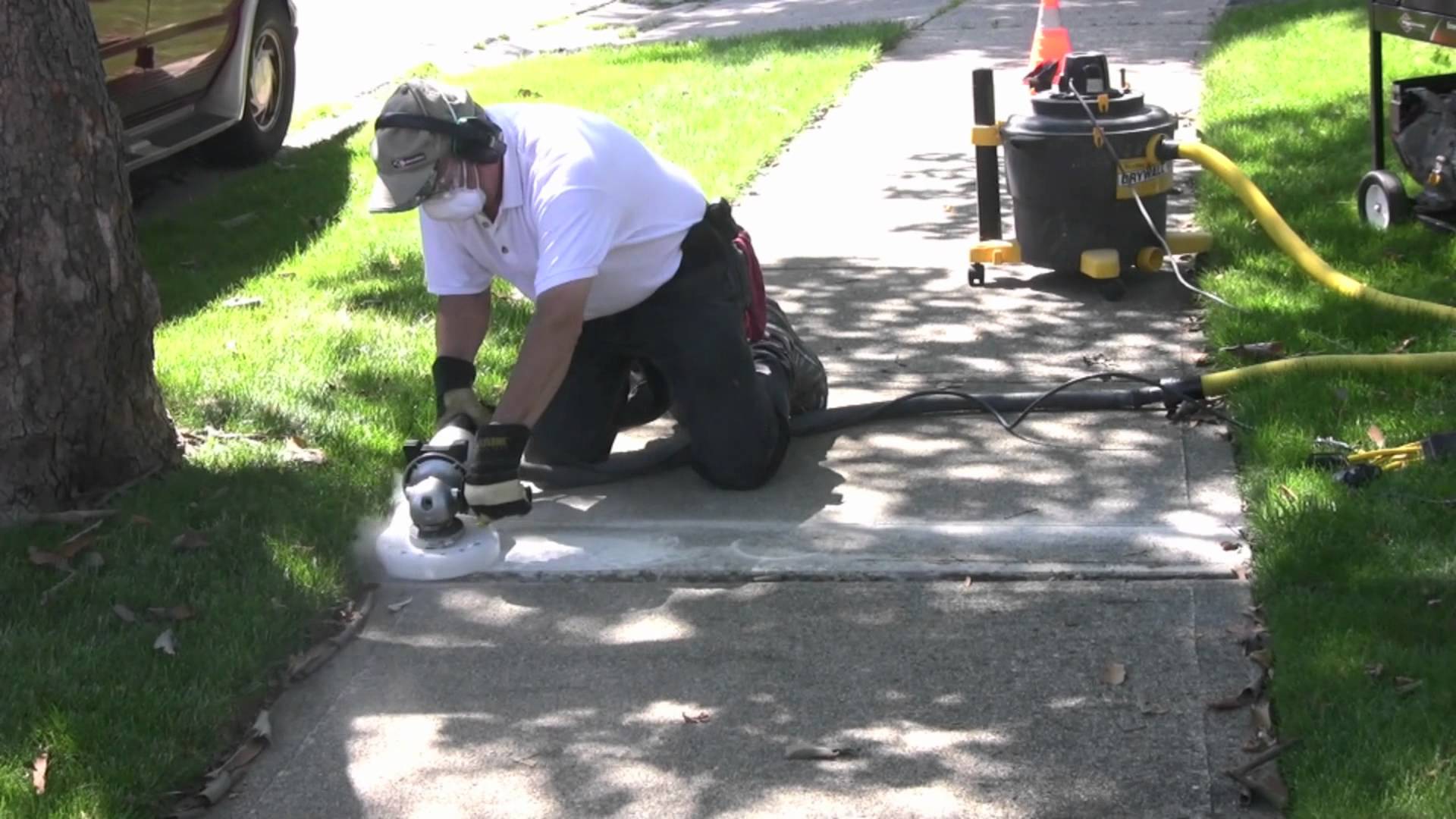
Grinding is another way that you can eliminate a trip hazard. However it does not solve the underlying issue and is needed regularly to maintain. Grinding involves grinding off a portion of the good concrete slab so it matches the sunken slab. Grinding is a short term solution. Read more information on grinding below.
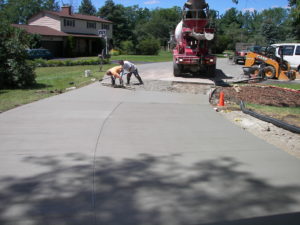
Replacement is the most expensive of the slab foundation repair methods. It is also incredibly disruptive and could lead to multiple problems in other areas of the structure if not properly braced during the removal of the slab.
Does Grinding Work?
The Truth About Grinding:
There are companies who grind off the lip of a good slab to fix a Trip Hazard. Think of this logically. Something happened to cause the settling in the first place. One area sunk down causing the hazard.
Will grinding off the good section solve the problem? No, grinding down the good section NEVER, EVER fixes the root of the problem. It doesn't address the issue and causes other problems.
Services that promote grinding as a fix for trip hazards usually have not been around long enough to understand that the problem will return, and usually the very next year.
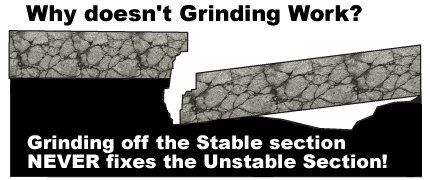
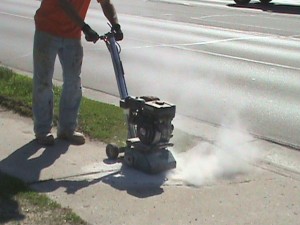
Usually What Happens With Grinding:
1. A facility pays to grind the good slab to match the bad. This removes the trip hazard temporarily.
2. As the bad slab continues to settle and move, over time that trip hazard returns (usually within a year) and the facility then pays to grind again. This again removes the trip hazard.
3. However since the root of the problem is not being addressed the bad slab will continue to settle and move and the grinding cycle continues costing money each time.
https://www.traditionrolex.com/42
4. Eventually both the good and bad sections must be replaced because the good section has been ground down to the point its too thin to support weight. Since the sinking issue was never addressed there is also a major depression causing water ponding.
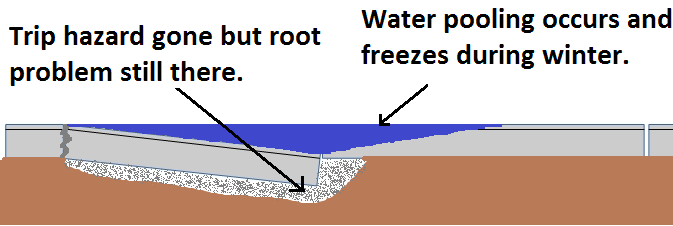
Bottom Line:
If you are very tight on funds, grinding could be a solution for you. Just remember that it is a short term fix that eventually will lead to the replacement of at least 2 concrete slabs.

Cost of Repair:
Other than the high cost of slab replacement, the cost of repair varies greatly between the foundation raising methods; given that each method varies greatly in the disruption it causes to the use of the structure.
Costs are influenced by other factors including but not limited to:
* The location of the structure
* The condition of the foundation,
* The characteristics of the underlying soil
* The expense of the material being used.
Mudjacking VS Polyjacking... Pros & Cons
MUDJACKING
Pros
• Less expensive - Mudjacking is less expensive than polyurethane concrete raising, so it may be a good choice if you’re on a tight budget.
• Familiar process - Many foundation repair companies are familiar with mudjacking because the process has been around so much longer.
Cons
• Shorter lifespan - Mudjacking won’t last as long because the fill materials will eventually lose density.
• Heavier - The fill is heavier, creating more of a burden on the soil.
• More noticeable - Because the fill material is heavier, more and larger injection holes are required. This is problematic when the repair work is being done on a visible surface, such as a concrete slab or sidewalk.
POLYJACKING
Pros
• Lasts longer - Polyurethane concrete raising lasts much longer because the material never loses its density.
• Lightweight - The lightweight polyurethane fill creates less of a burden on the soil than mudjacking.
• Nearly invisible - Because the material is so lightweight, fewer and smaller injection holes are required, making it difficult to tell that repair work has been done.
Cons
• More expensive - Polyurethane concrete raising is more expensive. If you’re on a tight budget, it may not be the best option.
• Newer process - Because the process has only recently been applied to residential applications, you may have a tough time finding a qualified professional in your area.
Additional Benefits of Polyurethane Foam
Cost Effective: Concrete raising is typically about half the cost of replacing the same concrete. Ultimately, the cost of raising or stabilizing concrete with polyurethane is a direct reflection of how much leveling material the project will require.
Time: Ready to use immediately!
Clean Work Environment: No concrete or grout splatter and no wash down needed.
Smaller Holes: Polyurethane concrete raising drills a nearly invisible 5/8 inch hole and the process calls for considerably fewer holes than traditional mudjacking; Minimal patchwork is needed.
Lightweight: This material will never lose density, is permanent and weighs only about 2 lbs. per cubic foot. Compared to traditional Mudjacking material, which weighs on average 100 lbs per cubic foot.
Green: The poly foams we use are environmentally friendly, consisting of 39-49% renewable and recycled materials. This foam is a top-of-the-line material, designed specifically for different concrete applications, it allows us to easily adjust our approach to your needs.


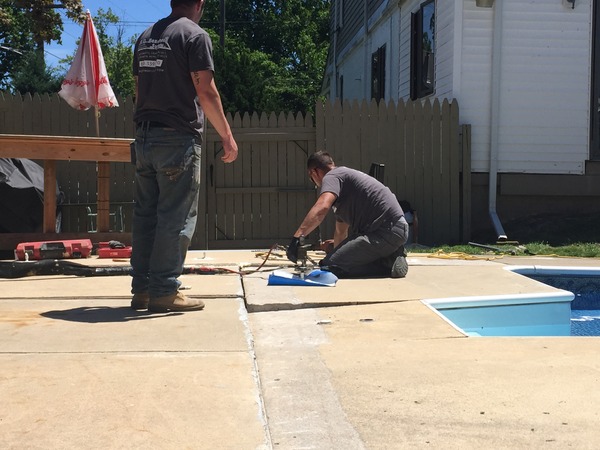
Methods of Concrete and Foundation Repair
What if you could raise a cracked or sunken slab back to its proper level in less than an hour, with no “down” time waiting for new concrete or mortar to cure?
There are only three choices when it comes to repairing a settled or sunken concrete slab: replace it, grind it, or raise it. Before the use of polyurethane and Poly jacking, the common methods of raising and supporting a slab was by mudjacking.
Following is a brief description of the options to consider when you're raising a sunken slab.
Poly Jacking
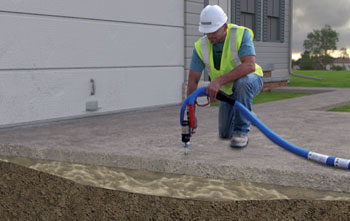
Poly Jacking, also called Foam jacking, lifts and raises settled slab foundations by injecting high density polyurethane foam under the slab, where it expands and pushes the slab back into place. The lifting is gentle and over a large area at once, which helps to ensure the most complete lifting of all the methods.
Mudjacking
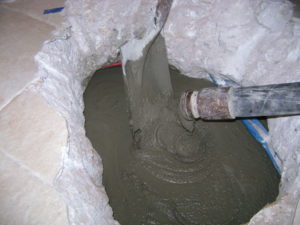
Mudjacking, also called Slabjacking, lifts and raises settled slab foundations by pumping sand-based grout under the slab. The mechanical force of the pump pushes the slab back into place. Mud jacking tends to be pretty messy, and is best used for unoccupied areas of the home.
Grinding
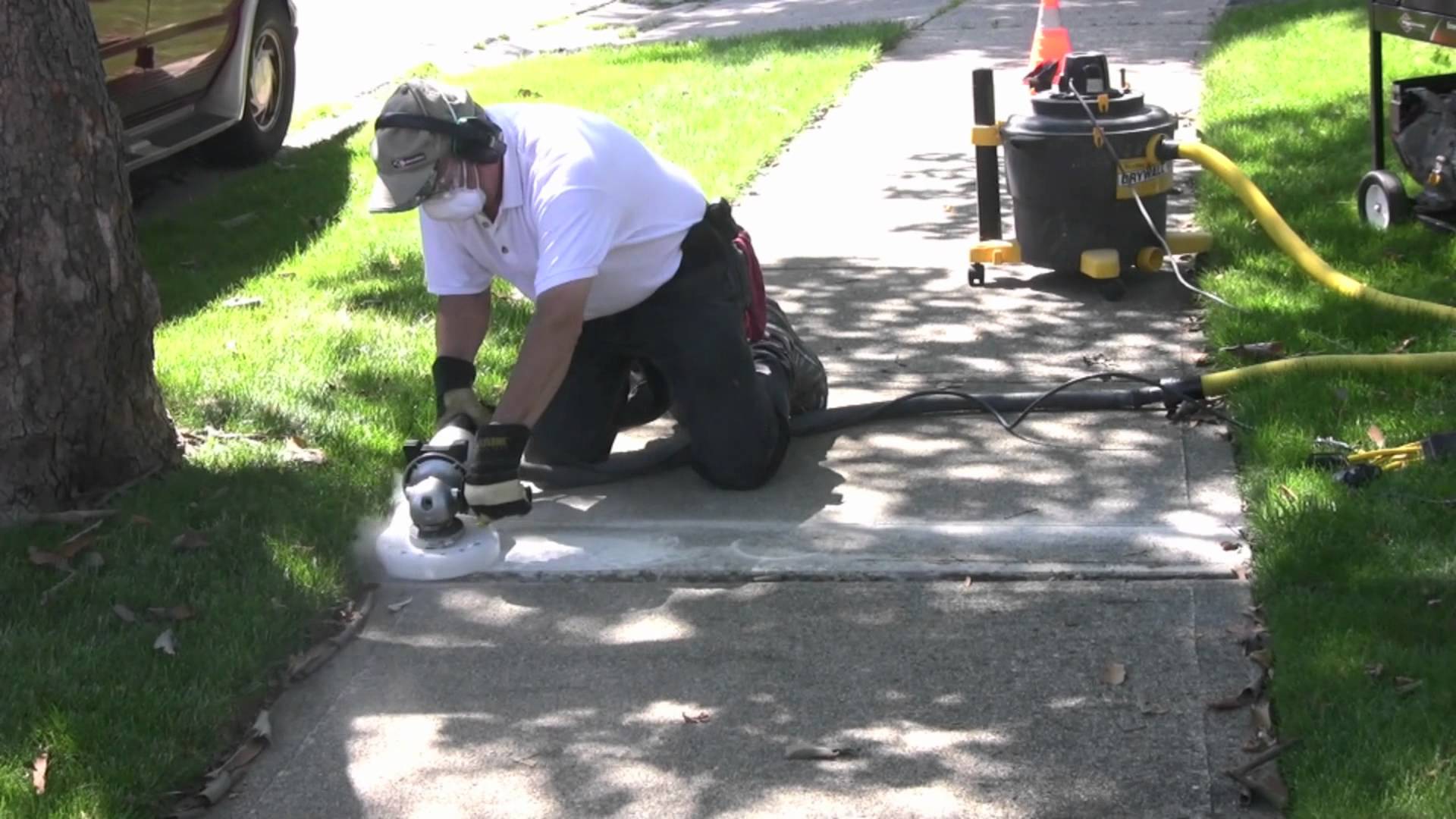
Grinding is another way that you can eliminate a trip hazard. However it does not solve the underlying issue and is needed regularly to maintain. Grinding involves grinding off a portion of the good concrete slab so it matches the sunken slab. Grinding is a short term solution. Read more information on grinding below.
Replacement
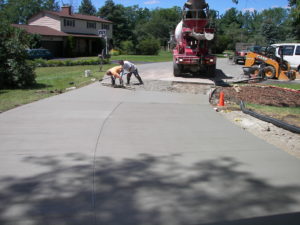
Replacement is the most expensive of the slab foundation repair methods. It is also incredibly disruptive and could lead to multiple problems in other areas of the structure if not properly braced during the removal of the slab.
Does Grinding Work?
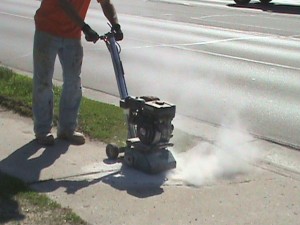
The Truth About Grinding:
There are companies who grind off the lip of a good slab to fix a Trip Hazard. Think of this logically. Something happened to cause the settling in the first place. One area sunk down causing the hazard.
Will grinding off the good section solve the problem? No, grinding down the good section NEVER, EVER fixes the root of the problem. It doesn't address the issue and causes other problems.
Services that promote grinding as a fix for trip hazards usually have not been around long enough to understand that the problem will return, and usually the very next year.
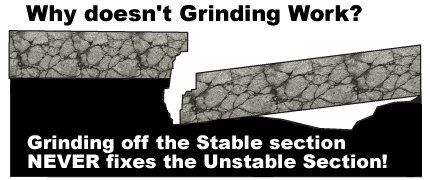
Usually What Happens With Grinding:
1. A facility pays to grind the good slab to match the bad. This removes the trip hazard temporarily.
2. As the bad slab continues to settle and move, over time that trip hazard returns (usually within a year) and the facility then pays to grind again. This again removes the trip hazard.
3. However since the root of the problem is not being addressed the bad slab will continue to settle and move and the grinding cycle continues costing money each time.
4. Eventually both the good and bad sections must be replaced because the good section has been ground down to the point its too thin to support weight. Since the sinking issue was never addressed there is also a major depression causing water ponding.
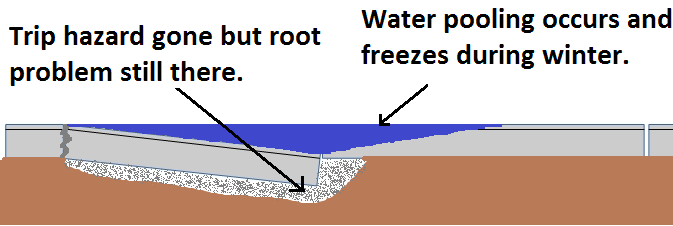
Bottom Line:
If you are very tight on funds, grinding could be a solution for you. Just remember that it is a short term fix that eventually will lead to the replacement of at least 2 concrete slabs.

Cost of Repair:
Other than the high cost of slab replacement, the cost of repair varies greatly between the foundation raising methods; given that each method varies greatly in the disruption it causes to the use of the structure.
Costs are influenced by other factors including but not limited to:
* The location of the structure
* The condition of the foundation,
* The characteristics of the underlying soil
* The expense of the material being used.
Mudjacking VS Polyjacking... Pros & Cons
MUDJACKING
Pros
• Less expensive - Mudjacking is less expensive than polyurethane concrete raising, so it may be a good choice if you’re on a tight budget.
• Familiar process - Many foundation repair companies are familiar with mudjacking because the process has been around so much longer.
Cons
• Shorter lifespan - Mudjacking won’t last as long because the fill materials will eventually lose density.
• Heavier - The fill is heavier, creating more of a burden on the soil.
• More noticeable - Because the fill material is heavier, more and larger injection holes are required. This is problematic when the repair work is being done on a visible surface, such as a concrete slab or sidewalk.
POLYJACKING
Pros
• Lasts longer - Polyurethane concrete raising lasts much longer because the material never loses its density.
• Lightweight - The lightweight polyurethane fill creates less of a burden on the soil than mudjacking.
• Nearly invisible - Because the material is so lightweight, fewer and smaller injection holes are required, making it difficult to tell that repair work has been done.
Cons
• More expensive - Polyurethane concrete raising is more expensive. If you’re on a tight budget, it may not be the best option.
• Newer process - Because the process has only recently been applied to residential applications, you may have a tough time finding a qualified professional in your area.
Additional Benefits of Polyurethane Foam
Cost Effective: Concrete raising is typically about half the cost of replacing the same concrete. Ultimately, the cost of raising or stabilizing concrete with polyurethane is a direct reflection of how much leveling material the project will require.
Time: Ready to use immediately!
Clean Work Environment: No concrete or grout splatter and no wash down needed.
Smaller Holes: Polyurethane concrete raising drills a nearly invisible 5/8 inch hole and the process calls for considerably fewer holes than traditional mudjacking; Minimal patchwork is needed.
Lightweight: This material will never lose density, is permanent and weighs only about 2 lbs. per cubic foot. Compared to traditional Mudjacking material, which weighs on average 100 lbs per cubic foot.
Green: The poly foams we use are environmentally friendly, consisting of 39-49% renewable and recycled materials. This foam is a top-of-the-line material, designed specifically for different concrete applications, it allows us to easily adjust our approach to your needs.

